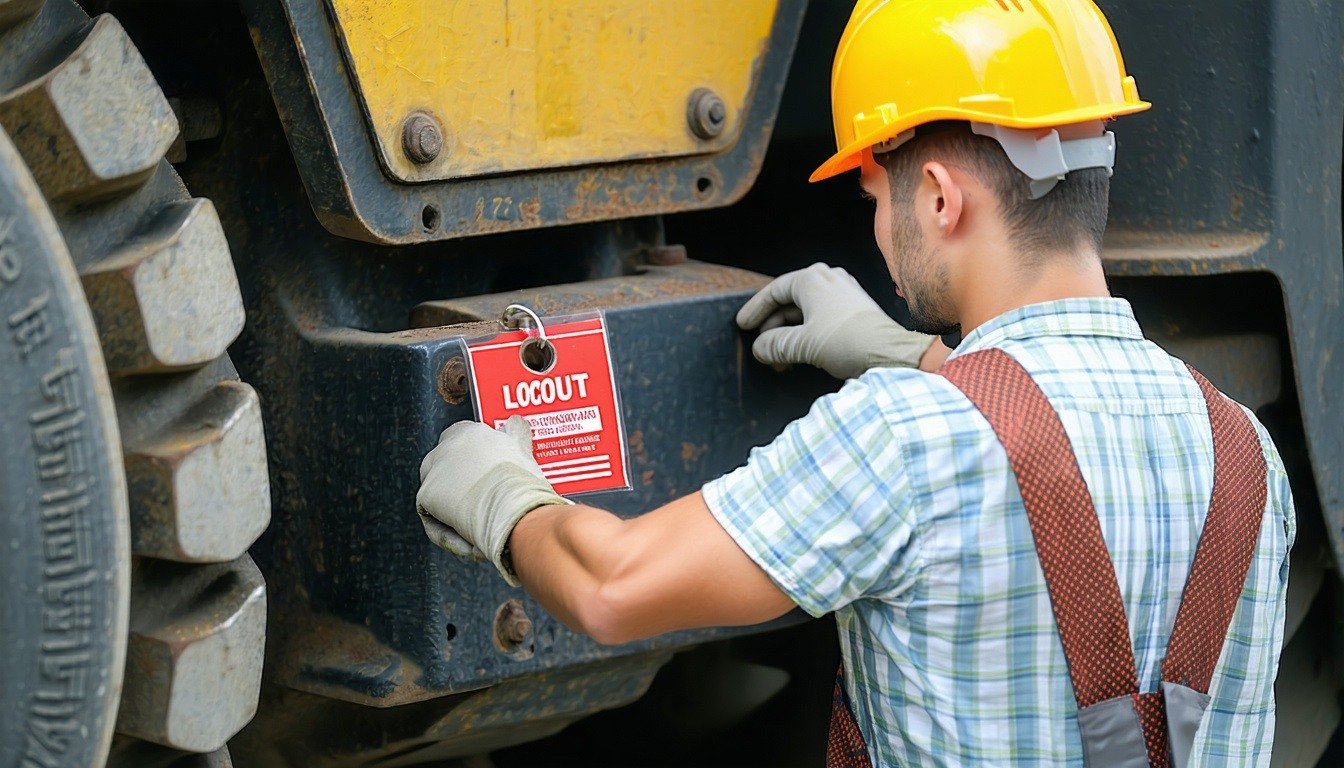
Lockout Tagout (LOTO) procedures are essential for ensuring the safety of employees in construction and manufacturing environments, where the risks of machinery-related accidents are high.
Understanding Lockout Tagout: What It Is and Why It Matters
Lockout Tagout, often abbreviated as LOTO, is a safety procedure used to ensure that dangerous machines are properly shut off and not started up again before the completion of maintenance or repair work. This involves the use of locks and tags to isolate and secure hazardous energy sources, preventing accidental or unauthorized activation of machinery. For more detailed guidance, explore our Lockout Tagout Training.
The importance of LOTO cannot be overstated. It is a critical safety measure designed to protect employees from the dangers of unexpected energization or the release of stored energy. In industries like construction and manufacturing, where heavy machinery and complex equipment are commonplace, the risks associated with improper handling of these machines are significant. Implementing LOTO procedures helps mitigate these risks, ensuring a safer work environment.
The Consequences of Ignoring Lockout Tagout Procedures
Ignoring LOTO procedures can have severe consequences, both for employees and the organization. The most immediate risk is physical harm to workers. Without proper LOTO protocols, there is a heightened risk of machinery starting unexpectedly, which can lead to serious injuries or even fatalities.
Beyond the human cost, there are significant financial repercussions. Workplace accidents can result in costly medical expenses, workers' compensation claims, and potential lawsuits. Additionally, the operational disruptions caused by accidents can lead to downtime, affecting productivity and potentially damaging the company's reputation. Ensuring strict adherence to LOTO procedures is not just a regulatory obligation but a moral and financial imperative. For more insights and guidance, explore our Lockout Tagout Training.
Key Components of an Effective Lockout Tagout Program
An effective LOTO program consists of several key components. First and foremost is the development of a comprehensive LOTO policy that outlines the procedures and responsibilities for locking and tagging out machinery. This policy should be clearly communicated to all employees and regularly reviewed and updated. For more detailed guidance, explore our Lockout Tagout Training.
Training is another critical component. Employees must be educated on the importance of LOTO, the specific procedures to follow, and how to identify and control hazardous energy sources. Regular training sessions and refresher courses help ensure that all staff members are knowledgeable and compliant. To enhance your safety training program, consider implementing gamification techniques for better learning outcomes, which can significantly improve engagement and retention of safety procedures.
Additionally, proper documentation is essential. Detailed records of all LOTO activities should be maintained, including logs of equipment lockouts, maintenance schedules, and any incidents or near-misses. This documentation not only ensures compliance but also helps identify areas for improvement in the LOTO program.
How Technology Can Enhance Lockout Tagout Compliance
Technology can play a pivotal role in enhancing LOTO compliance and improving overall safety. Digital LOTO systems, for instance, can streamline the management of lockout procedures by providing real-time tracking and documentation. These systems can generate automatic alerts and reminders for scheduled maintenance, ensuring that no steps are missed.
Mobile applications can also be used to provide on-the-go access to LOTO procedures and checklists, making it easier for employees to follow the correct steps and verify compliance. Additionally, advancements in wearable technology can help monitor employee movements and machine statuses, providing an added layer of safety and accountability.
By leveraging technology, organizations can create more efficient and effective LOTO programs, ultimately reducing the risk of accidents and enhancing workplace safety.
10 Practical Lockout Tagout Tips for Safety Directors
1. Develop a Clear LOTO Policy: Ensure that your LOTO policy is comprehensive, easily accessible, and regularly updated.
2. Conduct Regular Training: Provide ongoing training sessions to keep employees informed about LOTO procedures and the importance of compliance.
3. Use Standardized Equipment: Utilize standardized locks, tags, and devices to avoid confusion and ensure consistency across the organization.
4. Perform Routine Audits: Conduct regular audits of your LOTO program to identify any gaps or areas for improvement.
5. Engage Employees: Involve employees in the development and review of LOTO procedures to ensure they are practical and effective.
6. Document Everything: Keep detailed records of all LOTO activities, including maintenance logs, training sessions, and incident reports.
7. Leverage Technology: Implement digital tools and mobile apps to streamline LOTO procedures and enhance compliance.
8. Establish a Reporting System: Encourage employees to report any LOTO-related issues or near-misses to address problems promptly.
9. Ensure Proper Supervision: Assign supervisors to oversee LOTO activities and ensure that procedures are being followed correctly.
10. Promote a Safety Culture: Foster a workplace culture that prioritizes safety and encourages adherence to LOTO procedures at all times. Consider implementing safety training incentives to motivate employees and reinforce the importance of safety practices.
Leave a Comment