Humtown Products targets improvements in shop floor communications and employee productivity with Ving.
Humtown employees benefit from using Ving!
They have some of the same challenges that many other companies have.
-
Paper-based information sharing of manufacturing processes made it hard to keep documentation up-to-date; employees were often working with dated information
-
Outdated information made quality control standards hard to maintain
-
Accessing and reading large, paper-based process documentation was cumbersome and time-consuming for employees on the floor; productivity was hindered and morale was affected
-
Management was unable to track which team members had accessed the most up to date information
With these problems outlined Humtown was looking for a solution and found Ving.
-
Once documentation of manufacturing processes was uploaded to Ving, updates to any information and instructions are easily made in real time
-
Up-to-date process documentation, as well as quality alerts for specific parts, is available to all floor employees at any time; they now begin every job knowing exactly what to do
-
Productivity and quality have been vastly improved through Ving’s digital packets, which include diagrams, video and other visual documents
Here is a little more about Humtown Products.
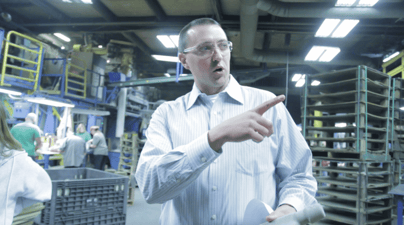
Humtown Products is a full-service supplier to manufacturers of metal castings, also known as the foundry industry. The family-owned business was established as a pattern shop in 1959, at which time Humtown earned a reputation for superb craftsmanship and attention to detail. That reputation grew right along with the company as it began serving the core making needs of foundries throughout the Midwest. Along with meeting the conventional core making needs, Humtown now provides 3D Sand Printing services. Humtown Products contributes to the manufacturing of parts and equipment used in a diverse array of industries, including: agriculture, construction, manufacturing, mining, national defense, public utilities, and transportation.
Humtown Business Challenges
Like any company in the manufacturing industry, Humtown has step-by-step process documentations for each Part that employees are required to follow on the production floor. Previously, Humtown workers only had access to information about these processes through large, paper-based documents that were housed in large binders near the production line.
“Before we had to leave our station, come check and find the paper that matched your machine, and then head back to the station. It wasted a lot of time,” said Jacob Fitch, a machine operator at Humtown.
When updates to the documents were made – which was a cumbersome process on its own – it was incumbent on the workers to read through the manuals, and find and understand the new information.
Humtown management had no way to track who was reading the updates as they became available, which made quality control and assurance hard to manage. Additionally, worker productivity was significantly slowed down when employees had to sort through lengthy documents to hunt for new and updated information – which was also contributing to lower morale, as compensation is tied to employee productivity.
Brandon Lamoncha, Sales Manager and Solution Provider for Humtown said, “Our processes for sharing information were antiquated and contributed to inefficiencies that affected both throughput and workers’ ability to increase earnings. We knew we needed a better way. Luckily, we found Ving.”
The employees at Humtown completely agree.
“The quicker I can start a machine the more money I make so having a tool that allows me to start quicker means I can make more money,” said Ken Oberholtzer “There is less stress on me because I do not need to remember every detail. I can review the Ving before each station and I am ready to start the job.”
Moving to a paperless shop increases quality and productivity
When Brenda Covert, Marketing and Sales, joined Humtown a few years ago, her colleagues at the company were already looking into deploying Ving to see how it might improve shop floor communications and efficiencies. “Going from a paper-based environment to paperless was a big goal, the management here recognized that the large volumes of process documentation made it hard for Team members to access and absorb all the information,” she said.
“With Ving, we simply upload the process documentations to the platform and make the URL for each document accessible to workers right from the shop floor,” she added. “It’s extremely easy for them to pull up and see new information, as well as receive quality alerts about particular parts, as soon as they’re available. And with the addition of short video clips that provide additional detail and direction, workers are well-informed before they start their jobs every single day.”
“Since putting Ving in place we’ve experienced three key benefits – quality improvement, Team morale and industry credibility. Having the most up-to-date information immediately available improves productivity and gives us a better handle on quality control, which was our main objective. An added bonus is that our customers are also impressed with how efficient our operations are, and that strengthens our reputation with them.”
Humtown employees say on top of getting the job done right it makes work less stressful and allows new employees to be trained quicker.
“Ving makes training new employees easy. They have something they can refer back to without having to worry about memorizing the details of every core. We love using Ving. It is the first thing I see and I never have any issues with it. I can easily get it on my phone and view whatever I need to — like the process sheets,” said Matt Hayward.
“Ving makes it easier to make a lot of different product for a lot of different companies. There is less to worry about memorizing because every day I know the Ving will be there first thing,” said Jacob Fitch.
What is next for Humtown?
In the future Humtown is looking at possibly adding some animations and other multimedia to Vings, to make the documentation content even more engaging.
“Real-time access to the most up-to-date information right from the machine employees are operating has been a huge boost to productivity, quality control, and even morale. Ving has brought incredible benefits to our team, and there will be more to come as we expand our use of the platform,” said Covert.
Leave a Comment